レーザー加工とは?種類やメリットについて
硬い素材も短い時間で美しく加工できるレーザー加工は、身近な家電から、製造業や建築業、医療現場などで幅広く利用されています。
レーザー加工に使われるレーザーの種類や加工方法には、多くの種類があり、加工の用途や目的、材料の特質などによって使い分けられています。
1900年代初頭に誕生し、少しずつ進化を遂げたレーザー加工の種類やメリット、デメリットなどを解説していきます。
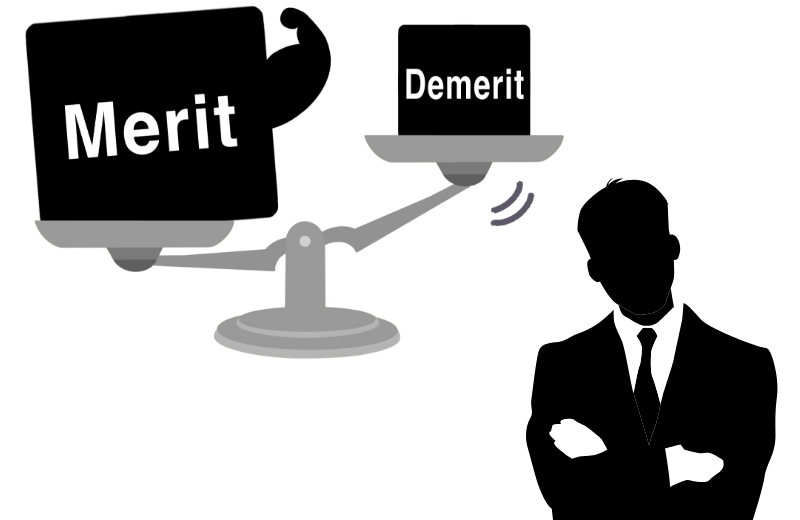
レーザー加工とは?
レーザー加工とは、レーザーの光を金属などに照射し、カットや穴あけなどを行う加工方法です。
レーザー発振器から伝送されたレーザー光を集め、金属に照射して、その熱でレーザー光が集光されたところを溶かして切断し、アシストガスを吹き付け、溶融部を吹き飛ばしていきます。
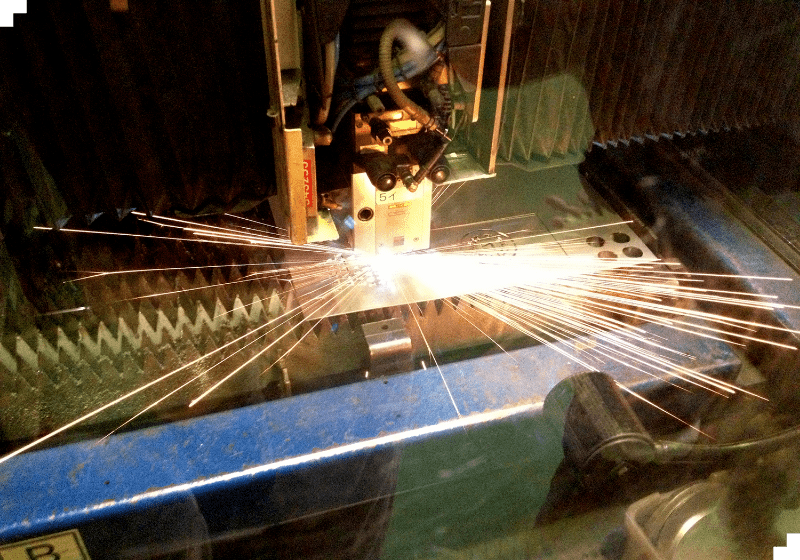
非接触で切断するので、材料に物理的な力を加えません。また、切断時の集光したレーザー光の幅がごく微小なので対象のワークへの熱影響が少なく、他の熱を加える加工に比べてワークが変形しにくくなっています。狭い切断幅なので他の切断方法に比べて寸法精度が出やすく精密な加工ができます。
レーザー加工に使用されるレーザー光は、人工的に作られた光です。
高密度なエネルギーを一点に集中できる特性があるため、加工の際の材料の硬さに左右されずに作業可能です。
レーザー加工機の内部にあるレンズによって焦点幅を定めることができ、レンズを絞るほどに極小スポットになり、かなり精密な加工も可能になります。
加工できる素材は金属だけではなく、木材やゴム素材、布など幅広く、製造業をはじめ、建築のための木材の加工や衣類の生地の裁断、彫刻や装飾、医療現場での検査や手術など、多くの分野で活用されています。
レーザー加工の原理と仕組み
レーザー加工は、レーザー加工機内部にあるレンズにレーザー光を集めて、密度の高い光を作り、材料に合わせて出力などを調節しながら加工できる仕組みになっています。
光には、指向性と単色性、可干渉性の3つの要素があります。
指向性 | 音、電波、光などを空間中に出力するときの直進性 |
---|---|
単色性 | 光の波長の安定性 |
可干渉性 | 光の波長の山と谷の位相 |
レーザー光は、一般的な太陽光や電灯のような光と比べると、指向性、単色性、位相が一定に揃って安定しているため、一点に集中しやすく、さらにレーザー加工機内部にあるレンズで集光するので、金属を溶かすほどの威力になります。
レーザー加工でできること・できないこと
レーザー加工でできること
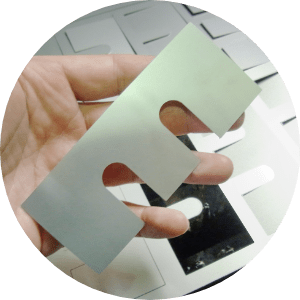
カットする
硬い材料から柔らかい材料までスピーディーにカットできます。
特にアクリルや木材、布などの素材に対して優れたカット力を発揮します。
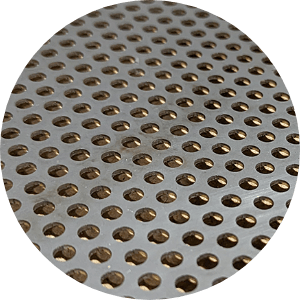
穴を開ける
鋼材をカットしやすくするため、または部品などの作成のためにレーザーで穴を開けることができます。

印を付ける
ガラスや木材、プラスチック、大理石などの幅広い素材に対して刻印することができます。アクセサリーなどの刻印もレーザーで行われることが多いです。
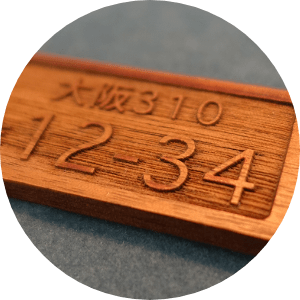
彫刻をする
溝を作ったり印をつけたりできる延長線上で、彫刻も可能です。
様々な素材に対して立体感ある彫刻が可能なので、表札や看板、写真などの作成によく用いられます。
レーザー加工でできないこと・苦手なこと
石やガラスをカットする
石やガラスに対しての彫刻は可能ですが、カットはできません。
多くの紙を重ねてカットする
多くの紙を重ねて加工をすると紙の間に空気層ができ、発火の原因になるため、カットできません。
数枚の紙のカットは可能です。
鏡などを加工する
鏡などの反射率が高い素材は、レーザーを照射した時に光が反射することでレーザー加工ができなくなります。
そのため、加工する時は反射しない裏面から行います。
塩化ビニールやフッ素配合の材料を加工する
レーザー加工の際に有害なガスの発生する塩化ビニールやフッ素配合の材料は、加工自体はできたとしても、危険性が高いため、加工できません。
20ミリ以上の厚みは苦手です
一点集中型で高密度なエネルギーを集められるレーザーは硬い素材の加工もできますが、一般的に20mm以上の厚板に対しては、レーザーのエネルギーが素材の裏面まで通りにくいため、素材が分厚くなるほど加工が難しくなります。
(当社の場合、21mm以上のステンレスの厚板は対応できません)
反射率が高い素材には不向き
銅やアルミニウムなどの反射率が高い材料は、レーザーの光が反射することによって熱が逃げるため、レーザー加工機によっては加工できないことがあります。
当社で導入している最新のファイバーレーザーなら問題なく加工できます。
レーザー加工のメリット
作業を効率化できる
高エネルギーのレーザー光を使えば、どんな材料でもスピーディーに加工できるため、作業時間がかなり短縮できます。
また、金属などの材料を加工する場合、これまでは加工の形の設定のために金型のような専用の型が必要でした。
しかし、レーザー加工ではパソコンによって形の設定を行うため、金型なしで作業ができます。
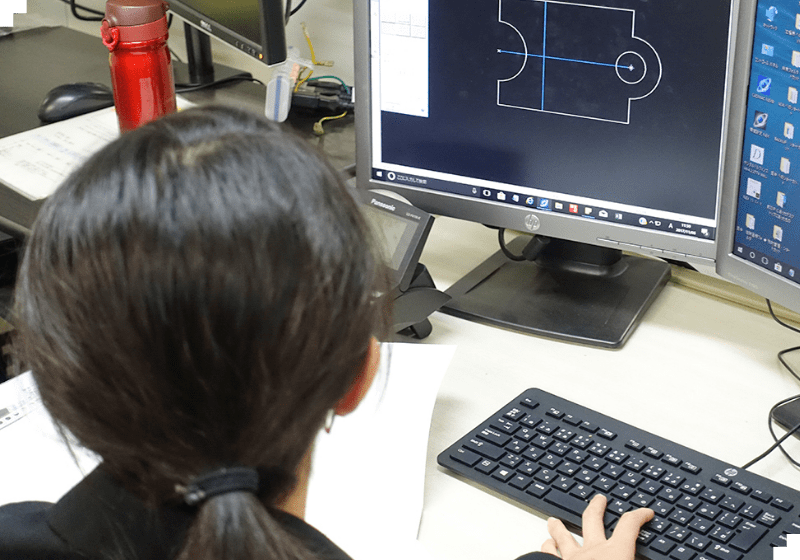
仕上がりが美しい
レーザー加工は、パワフルにスピーディーに作業できるだけではなく、仕上がりの美しさも高く評価されています。
これまでの作業で問題視されていたバリやカエリの発生を抑えることができ、切断面の仕上がりが非常にきれいです。
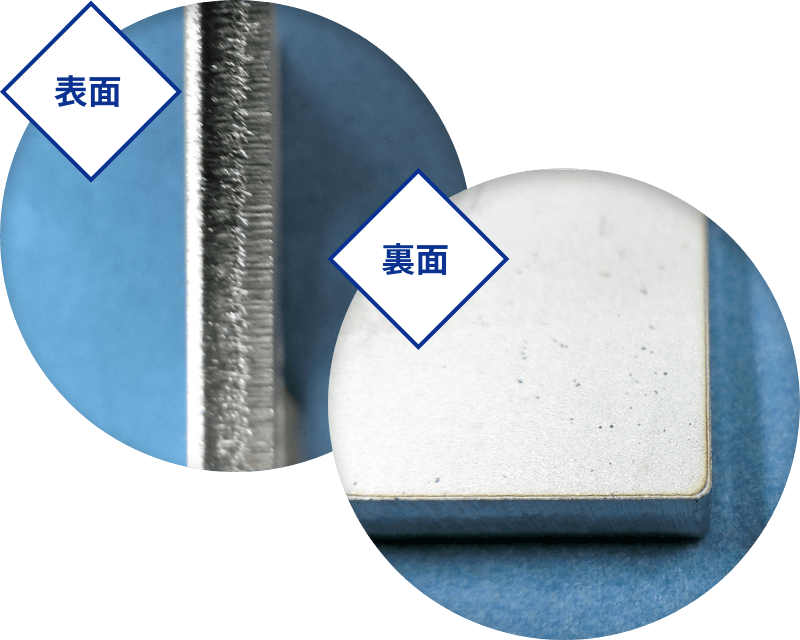
加工の自由度が高い
レーザー加工では、焦点位置やスポット径、光の出力などを設定することで、精密な加工が可能になり、自由度がかなり高いです。
硬すぎる金属から柔らかい素材まで、設定によって自由自在に加工できて便利に活用できます。
これまでは、熱を加えると変形していた姿の素材でも、レーザー導入により簡単にきれいに作業できるようになりました。
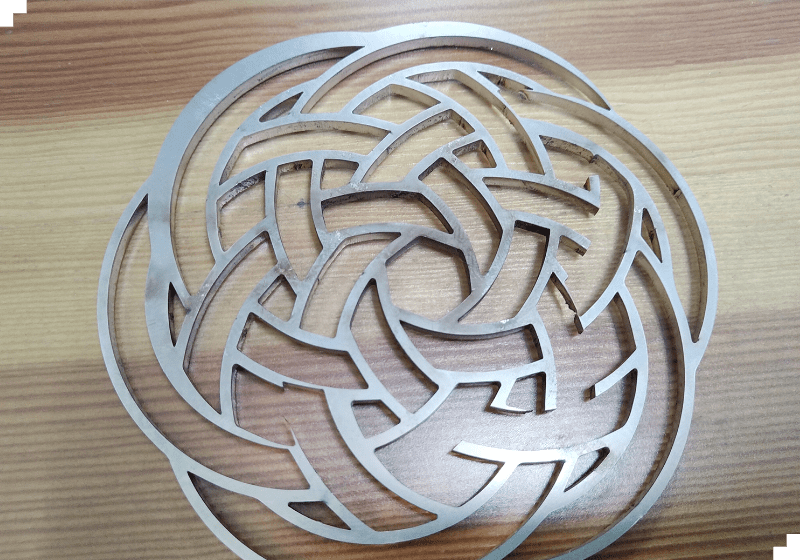
関連する最新の実績
レーザー加工の歴史
現在のレーザー加工に生かされているレーザー技術は、1917年にアルバート・アインシュタインが提唱したレーザーの基礎概念である「光の誘導放出論」がきっかけで誕生しました。
「光の誘導放出論」では、自然発生の光を意味する自然放出と、人工的に光を放出できる誘導放出の2種類の放出が提唱されました。
それまでの光の放出の常識では、自然発生の光の放出しか存在しないと思われていましたが、アルバート・アインシュタインの提唱により、人工的に光が放出できる誘導放出の意識が高まったのです。
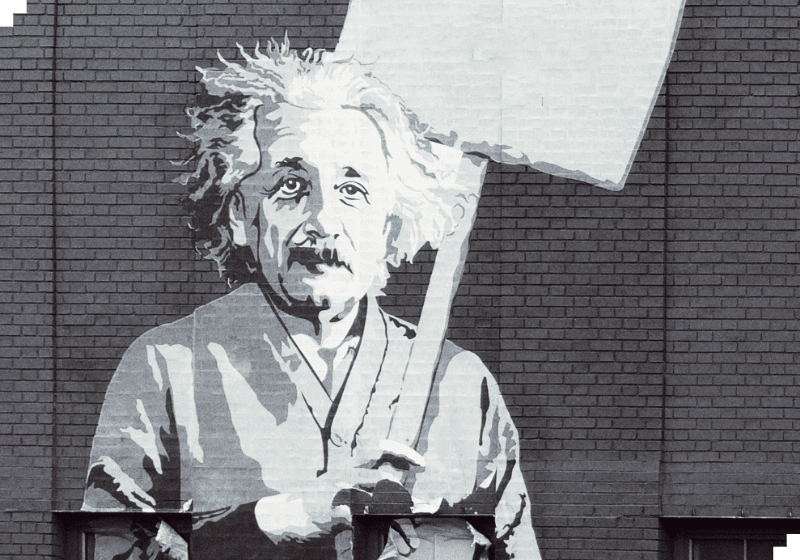
その後のレーザー技術の発展
1939年〜
その提供を受けて1939年には、レンティン・ファブリカントが放射増幅により、誘導放出の使用法を理論化し、1950年には、チャールズ・タウンズ、ニコライ・バソフ、アレクサンダー・プロクロフの3人が誘導放出の量子理論を確立しました。
さらに1959年には、コロンビア大学の大学院生だったゴードン・グールドが、光の増幅に誘導放出の利用が可能だと提唱し、そこからレーザーという言葉も誕生しました。
1960年〜
そして翌年の1960年、カリフォルニア州マリブにあるヒューズ研究所によって世界初のレーザーが製造されたのです。
この時のレーザーは、活性媒質に合成ルビーを使用したもので、軍事においての距離計測に活用されていました。
ダイヤモンドの穴あけに使えるほどのパワーを持つレーザーで、現在も使用されています。
1963年〜現在
1963年にはAT&Tベル研究所のクマール・パテルの開発により、低コストで高効率なCO2レーザーが誕生しました。
しかし、そのころのCO2レーザーは、出力はわずか1mW程度だったため、その後もCO2レーザーの改良が続き、1970年代には金属の切断や溶接が可能なレーザーへと発展していきました。
それ以降、固体や気体、液体、半導体を媒質としたレーザーが次々と誕生し、レーザー加工がより身近なものになりました。
加工に使うレーザーの種類
加工に使うレーザーは、固体や気体、液体などの媒体から生み出されて、様々な波長により種類が分かれています。
波長には、赤外線、可視光線、紫外線などがあり、それぞれに特徴があります。
固体や気体、液体などの媒体で分類した時、レーザーは次のような種類に分けられます。
固体レーザー
ファイバーレーザー
ファイバーレーザーは、コアに希土類元素を加えた光ファイバーをレーザー媒質とした形式のレーザーです。
光ファイバーは電気信号を光に変えて情報を伝達するケーブルで、インターネットの光回線でも有名になりました。
ファイバーレーザーの両端には、低反射ミラーと光反射ミラーがそれぞれに設置されており、励起光がファイバー内で反射しながら伝搬するうちに、コアにある希土類元素に吸収されてレーザー発振に至る仕組みになっています。
硬い素材の加工も得意とし、細くて深いレーザーを当てることができるので加工の自由度が高いです。
また、特徴としては銅、アルミなどの高反射材のカットや溶接もでき、熱による歪みを軽減する特徴もあります。
YAGレーザー
YAGレーザーとは、イットリウム(Y)、アルミニウム(A)、ガーネット(G)で構成された結晶をもとに生み出されたレーザーです。
イットリウムは、原子番号39の希土類元素に分類される遷移金属の一種で、銀白色の柔らかい素材です。
アルミニウムは一円玉でおなじみのアルミニウム合金で、ガーネットはマグネシウムや鉄、マンガンなどの珪酸塩鉱物で、石榴石(ざくろいし)とも言われている宝石の一種です。
これらの3つの構成物から生み出されたYAGレーザーは、美容クリニックなどの医療現場でも頻繁に使われています。
波長は1.06μmの赤外線レーザーで、レンズで集光すると金属加工ができるほど、威力を発揮するレーザー光になります。
1パルスあたりのエネルギーが調整できるため、カット加工や溶接加工では、歪みの少ない施工が可能で、ピアシングでは傾斜した穴加工にも対応できます。
気体レーザー
CO2レーザー
CO2レーザーは、二酸化炭素をレーザー媒質としたガスレーザーの一種で、金属や木材、アクリル、クリアなガラスなどの材料の加工に適しています。
医療現場では歯科治療や美容整形のレーザーとしても活用されています。
波長は10.6μmの赤外線レーザーで、10μm付近の波長に設定すると、ガラスのようなクリアな材料の加工にも対応でき、さらには柔らかい紙や木材などの加工にも活用できます。
一つのレーザー装置で、連続波とパルスでの出力を切り替えられるため、加工の自由度が高く使いやすいです。
エキシマレーザー
エキシマレーザーは、希ガスやハロゲンなどの混合ガスを媒質に生み出された紫外線レーザーで、レーザー装置は小型なのに高効率で発振できるため、工業や医療現場など様々な場面で活用されています。
医療現場においては視力矯正手術のレーシックが有名です。
エキシマレーザーの中にはいくつかの種類があり、次の3種類がよく知られています。
ArFエキシマレーザー(波長193nm)
KrFエキシマレーザー(波長248nm)
XeFエキシマレーザー(波長351nm)
レーザーカット加工やピアシング、スクライビングなど様々な加工法に適しています。
その他のレーザー
色素レーザー(液体レーザー)
色素レーザーは、エタノール、シクロヘキサン、トルエンなどを溶媒に溶かしてレーザー媒質とした液体レーザーの一種です。
色素の濃度や共振器の長さの変更により、波長を連続的に変化させることができ、物性研究やその他の分野でも広く活用されています。
GaNレーザー(半導体レーザー)
GaNレーザーは、別名で青色レーザーとも呼ばれている半導体レーザーの一種で、360nm〜480nmの波長を持っています。
有名な用途ではブルーレイをはじめ、高密度のオプトエレクトロニクスデータ記憶や医療現場での利用も盛んです。
自由電子レーザー
自由電子レーザーは、特定の原子間の結合に縛られず動き回れる自由電子のビームと電磁場の波動が共鳴してコヒーレント光を生み出す方式のレーザーで、波長を自由に変えられる特徴があります。
一般的なレーザーは、媒質によって発する光の波長が決まりますが、自由電子レーザーは操作によって自由に波長を変動でき、波長の種類も軟X線、紫外域、可視光線、遠赤外域まで幅広いです。
mWレベルの出力もできるため、兵器としての実用化を目指した研究も行われているほどです。
レーザー加工の種類
レーザー加工には7つの種類があり、用途によって加工法が使い分けられています。
1.レーザーカット
レーザーカットは材料にレーザーを照射することでカットする加工法をレーザーカットと言います。
金属などの硬い材料からプラスチックや木材、ゴム素材などの柔らかい材料のカットも可能です。2層以上の素材の場合は、上の層だけをカットすることができます。
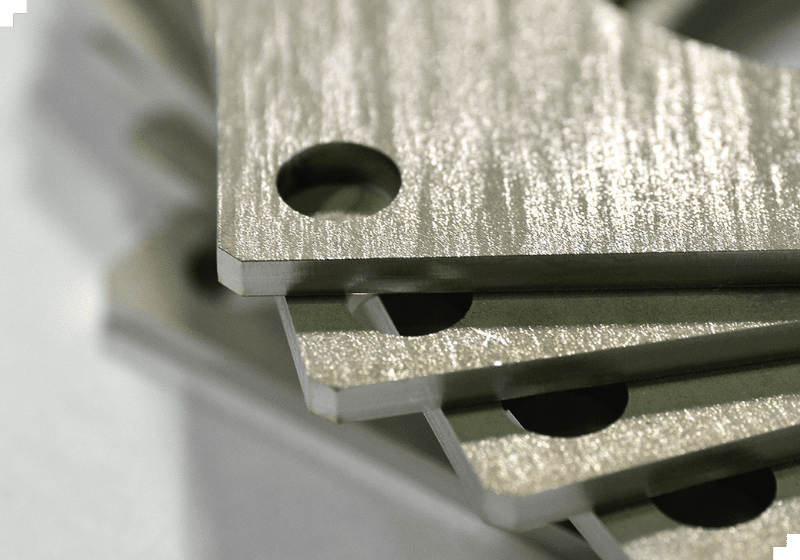
2.ピアシング
ピアシングとは穴あけ加工のことで、材料にレーザーを照射することによって、表面に溶融蒸発が起こり、穴あけをする加工方法です。
レーザー加工機内のレンズによって、レーザーを一点に照射することができ、熱エネルギーを集中させることで硬度の高い材料にも、穴あけが可能になります。
さらに熱エネルギーを微調整することができるので、精密な加工にも適しています。
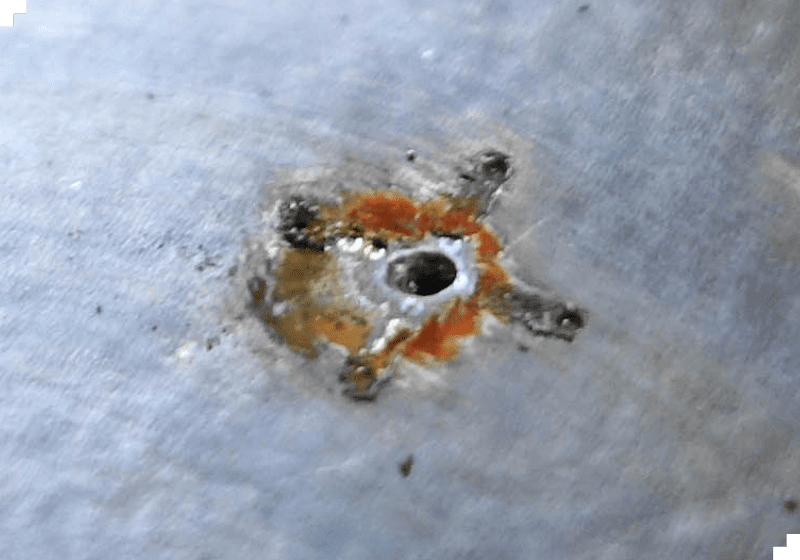
3.マーキング
レーザー加工のマーキングとは、分かりやすく言うと印をつける作業であり、切削や素材表面の色や反射率の変化させる方法で行われています。主に、バーコードや製造番号、ロゴ、イラスト、写真などによく用いられており、比較的低い出力で加工します。
最近では、塗料を使った一般的な印刷よりも、マーキング加工による印刷が注目されており、注目の理由としては、塗料の場合に発生する発色の劣化がないことが挙げられます。

4.レーザー彫刻
レーザー彫刻とはレーザーを使って彫刻する加工方法の一種です。彫刻刀で彫る時と同じようなタッチで立体的に線を描けて、金属などの硬い素材からプラスチック、ゴム素材、紙などの彫刻もできます。
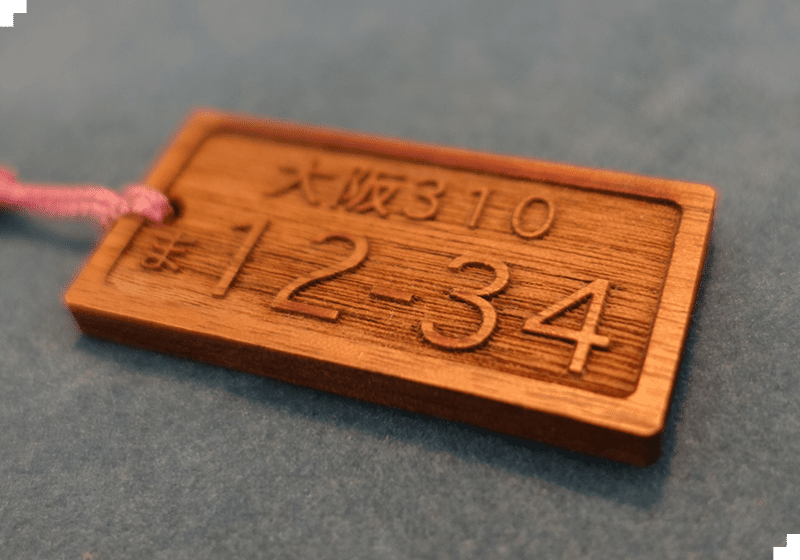
5.剥離
レーザーを使って樹脂の表面の塗装や対象とする物質の表面のメッキや皮膜などを除去する加工方法を剥離と言います。
レーザーを使用することによって、素早くきれいに剥離でき、樹皮や対象とする物質の表面をなるべく傷つけない作業が可能です。
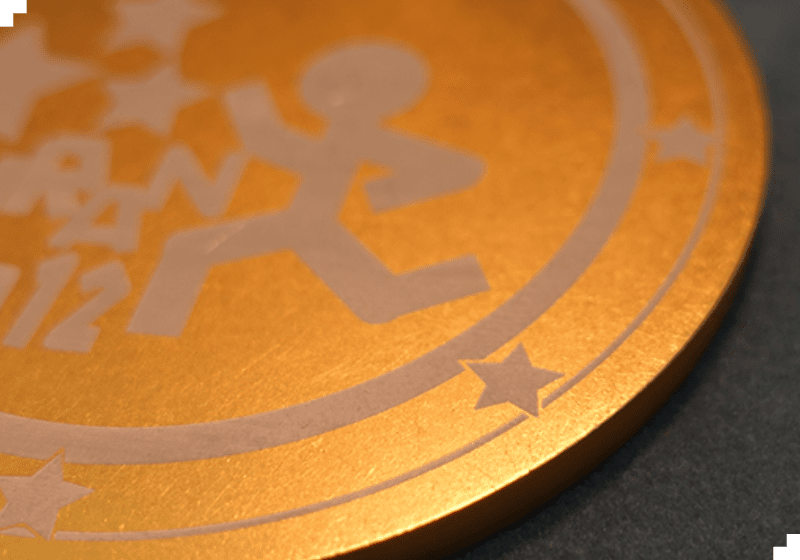
6.スクライビング
材料の表面に細かい亀裂や溝を作る加工をスクライビングと言います。
主にセラミックやガラスなどの硬い素材を切断する時に使われる加工方法です。
7.トリミング
トリミングは半導体分野でよく活用されている加工方法で、抵抗値変化を計測しながらチップ部品をカットする時に用いられます。
材料別のレーザーカット加工
レーザーカット加工をする際、材料によって設定などを変える必要があります。
鋼材のレーザーカット加工
鋼材とは、建築や土木関係、機械を扱う工業などの鋼鉄製の材料です。
用途に合わせて、スティックや筒、板状に加工をするのが一般的で、加工の際にはレーザーカットが用いられることが多いです。
レーザー加工の際には、材料の切断面に対して焦点位置を決める必要があります。(左記の図)
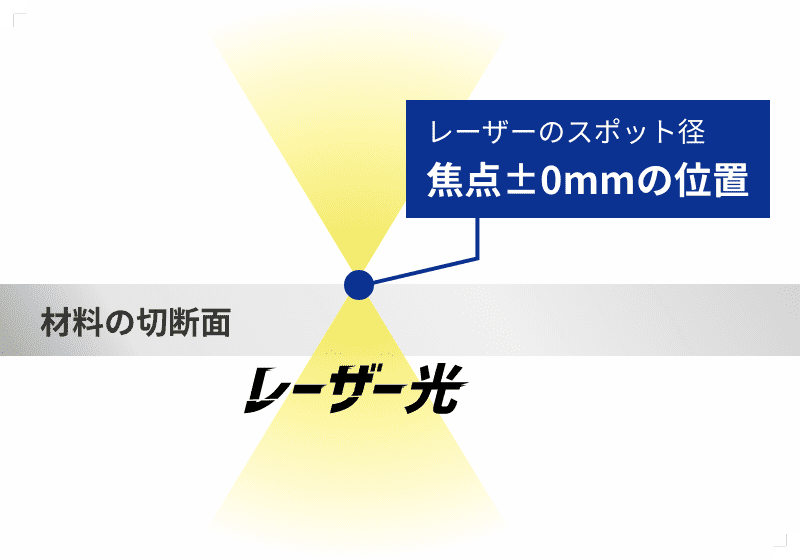
レーザー加工においての焦点位置とは、レーザーを当てたい場所で、レーザー加工機のレンズを動かし設定します。
焦点の位置を定めるときは、レーザーのスポット径が1番小さくなる焦点±0mmの位置に合わせます。
レーザーのスポット径が鋼材に当たる焦点位置によって、切断面が変わります。
ステンレスのレーザーカット加工
ステンレスとは、クロムとニッケルを含む錆びない鋼材で、鉄よりも硬くて丈夫な素材ですが、レーザーカット加工では素早く綺麗にカットできます。
通常レーザー加工ではガスとして酸素を使いますが、その場合、切断面に酸化皮膜が発生して焦げてしまい、焦げを削るなどの後加工が必要となってしまいます。
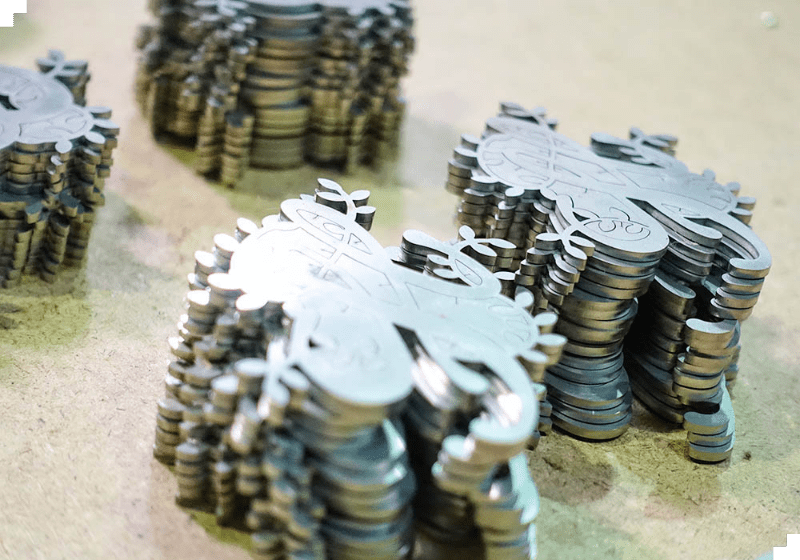
そこで、「クリーンカット(N2切断・窒素切断)」という手法が用いられます。
窒素をアシストガスとして使うことで、切断面を酸化させず、酸化皮膜(焦げ)の発生を防ぐことができます。
そのためきれいな銀色の状態でカットでき、酸化被膜の除去などの後加工も不要となって工数の削減に繋がります。
レーザー超特急24で行うステンレスレーザー切断の場合
切断時のアシストガスはすべて、窒素ガスを使用しており、クリーンカットで行っております。
そのため、切断面はすべて酸化被膜がない、ステンレス材特有のきれいな銀色の切断面となります。
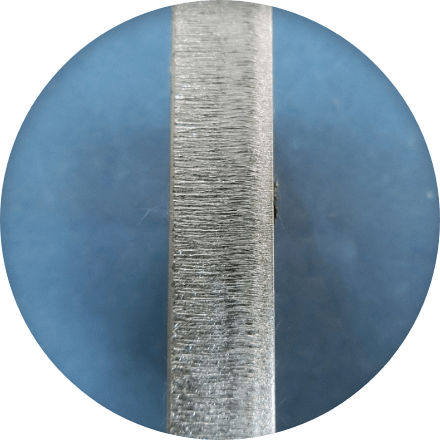
アルミニウムのレーザーカット加工
アルミニウムは、重さが鋼材の3分の1で非常に軽く、新幹線や家電などの軽量化のために幅広く使われている材料です。
アルミニウムのレーザーカットでは、レーザーの反射率が高いため、反射対策が施された加工機を使用することと板の厚さによって焦点距離を調節する必要があります。

特に板が厚い場合は、レーザーの熱で溶けて固まったドロスという溶融物が発生しやすいので注意が必要です。
焦点位置は、通常よりもかなり下の-5mmが最適で、焦点距離の調節により切断幅を広くすることで、アシストガスにより発生した溶融物の除去がスムーズになります。
薄い板の場合は、ドロス発生率が低いため、焦点±0mmでスムーズに作業ができます。
アクリルのレーザーカット加工
アクリルとは、合成樹脂の一種でアクリル樹脂と呼ばれるものです。
軽くて丈夫、透明度が高い特性を生かしてフォトフレームやテーブルマット、水槽の窓などによく使用されています。
CO2レーザー加工機でカットする場合は、アクリルのレーザー吸収率が高いため、スムーズに作業できます。
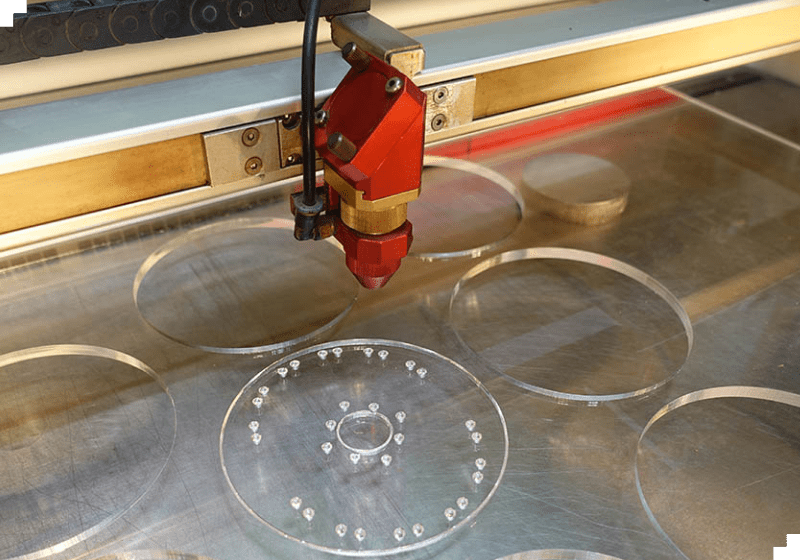
アクリルは熱に弱いので、レーザー加工の時に使うアシストガスに酸素を利用する場合は、火災に充分注意する必要があります。
レーザーカット自体はスムーズに行えますが、アシストガスの圧力を高く設定しすぎると、切断面の上部が不透明になるので、アシストガスの圧力を0.02MPa以下の設定が推奨されています。
レーザー加工と他の加工方法を比較
レーザー加工の他にも、プラズマ切断やウォータージェット切断などさまざまな加工方法があります。
それぞれの加工方法にはメリットとデメリットがある中で、いくつかの観点からレーザー加工と他の加工方法を比較します。
切断速度で比較
高密度なエネルギーを一点に集中させられるレーザー加工は、切断の速度も早いです。
他の加工方法と比較すると、次のような結果になります。
レーザー加工 | ガス溶断 | プラズマ切断 | ウォータジェット 切断 |
フライス加工 |
---|---|---|---|---|
◯ | △ | ◯ | ◯ | × |
小穴加工で比較
材料に小さな穴を開ける作業の効率を比較すると、次のようになります。
レーザー加工 | ガス溶断 | プラズマ切断 | ウォータジェット 切断 |
フライス加工 |
---|---|---|---|---|
◯ | × | × | ◯ | △ |
切断面で比較
加工後の切断面の美しさの比較では、ウォータジェット切断とフライス加工がトップです。
レーザー加工 | ガス溶断 | プラズマ切断 | ウォータジェット 切断 |
フライス加工 |
---|---|---|---|---|
△ | △ | △ | ◯ | ◯ |
切断精度で比較
材料を切断する時の加工の自由度や精密な設定について比較すると、次のようになります。
レーザー加工 | ガス溶断 | プラズマ切断 | ウォータジェット 切断 |
フライス加工 |
---|---|---|---|---|
◯ | × | × | △ | ◯ |
厚板切断が得意かどうかで比較
ぶ厚い材料の切断が得意かどうかを比較すると、次のようになります。
レーザー加工 | ガス溶断 | プラズマ切断 | ウォータジェット 切断 |
フライス加工 |
---|---|---|---|---|
× | ◯ | ◯ | ◯ | △ |
当社のレーザー加工機の紹介
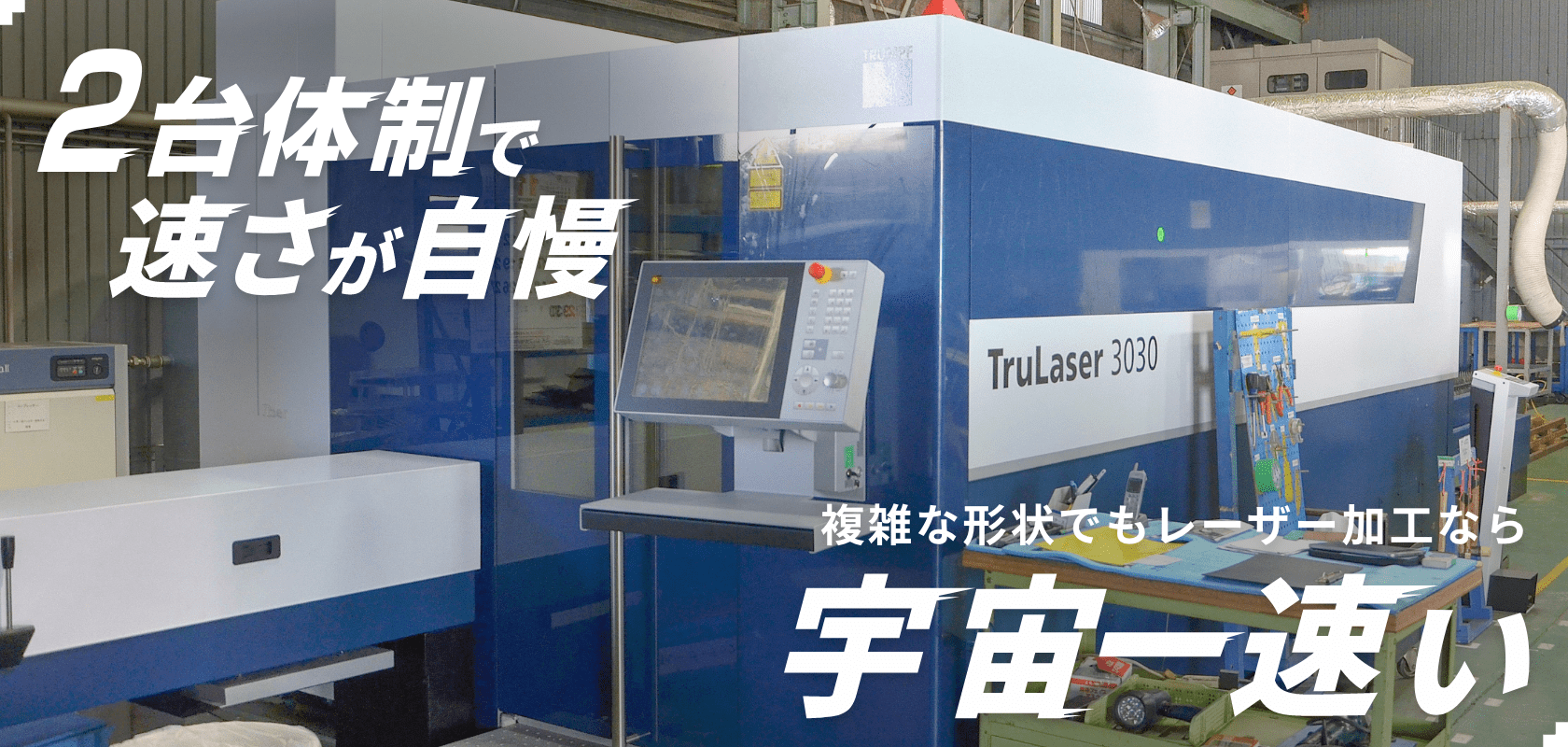
当社で使用しているレーザー加工機は、ドイツのトルンプ社の高性能高速レーザー加工機です。
トルンプ社は、日本ではあまりなじみのないメーカーですが、板金用工作機械メーカーとしては世界最大規模を誇るメーカーです。
特に、2015年に導入したファイバーレーザー加工機はさらに切断スピードがアップしているので、お客様のコストダウン要求にもお応えしやすくなっています。
また、レーザー加工機を2台持っていますので、急な機械の故障が起こってもバックアップ体制が整っております。
万が一2台同時に加工機が故障した場合も、機械メーカーに迅速に修理対応をしてもらい24時間以内に、復旧させる体制をとっております。
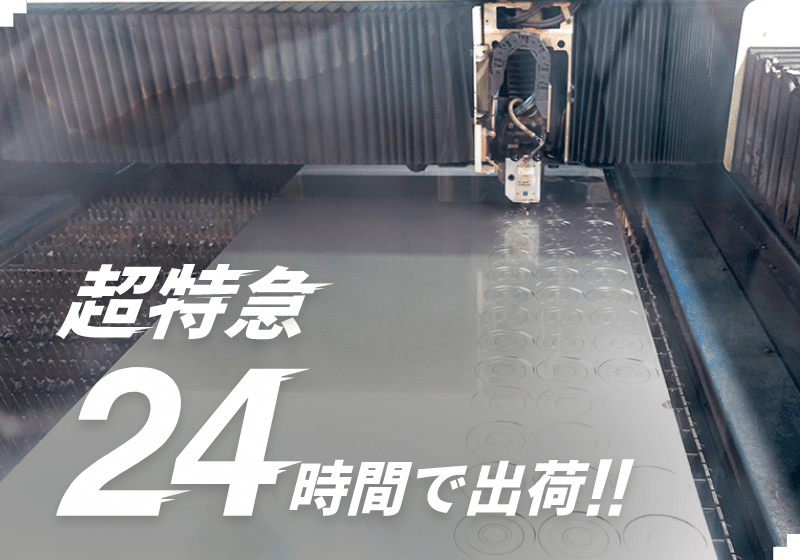
最新の実績はこちら
-
シムプレート大量品24時間で納入
枚数・個数: 合計1000枚 所要時間: 24時間 シムプレートステンレス -
ゴボ納品 イベントに間に合いました。
枚数・個数: 1枚(予備でもう1枚切断しました) 所要時間: 24時間 ステンレス文字複雑形状 -
6.0tステンレスリング特急引取
枚数・個数: 2枚 所要時間: 24時間 ステンレスリングレーザーカット